Resource Loading (input)
Figure 1 shows an example of manpower loading for a profitable
civil contract which was predominantly formwork and concrete placing.[1]
It displays a histogram of the make up and total numbers in the production work
force, week by week over a 38 week period. It also shows the progressive cumulative
total, or actual manpower loading S-curve. As noted earlier, the general profiles
of these curves appear to be quite typical (Christian 1991) whether the observations
refer to a whole construction project, a sub-contract, an individual trade or
a continuous construction activity of significant duration.
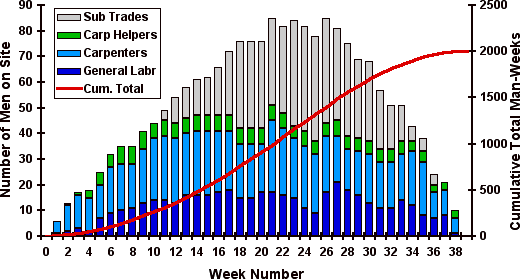
Figure 1: Civil contract example of site manpower (predominantly) concrete
work
The important points to note about the S-curve are that the initial part of
the curve represents the "build-up", the central part of the curve
is relatively "steady-state", or effectively a straight line slope,
and the latter part of the curve represents a "run-down" which closely
mirror-images the early part of the S-curve.
In order to understand the generality of the suggested rules of thumb that
follow, it is instructive to recite the many practical reasons for the shapes
of each of these three stages.
In Stage 1 there is an accelerating build up of manpower because
- Access to the work has to be opened up from a zero start, with the result
that the work itself becomes progressively more available.
- Necessary preliminary preparatory activities, including planning and understanding
local conditions, as well as ordering of materials, etc., often require fewer
people but more intensive supervision.
- Key people may be brought in to start the work, but supporting labour is
recruited locally. The recruiting and selection of local labour itself takes
time.
- With productive efficiency in mind, crews are added only as experience builds
and the work becomes available to be performed.
- Further crews are added only as pressure builds to get the job done within
the required time frame.
Stage 2 achieves a steady state because
- The working environment has reached optimum conditions for balanced performance
and repetition.
- Physical limitations to the capabilities of the men and equipment provided
is reached.
- Adding more labour or separate crews would over-crowd the working area and
reduce productivity.
- The number of repetitions available from which the benefits of "productivity
improvement" can be derived would be reduced.
- In either case the costs would be higher.
- Alternatively, if the work force is held at a lower level, the elapsed time
to accomplish the work will be prolonged, with consequent higher overheads and,
possibly, contract penalties to be faced.
These obvious trade-offs require careful management and balance.
In stage 3 almost the reverse of Stage 1 is true. Manpower is progressively
reduced because
- The work begins to run out.
- The remaining work space not occupied by following trades, or owner occupation,
runs the danger of becoming over crowded.
- Morale sometimes deteriorates as the end of the work is in sight and people
leave to join more active sites
- Less successful crews or individuals are let go first.
- The more difficult work may have been left to the end, may be more congested,
or otherwise require only the skills of those brought in initially.
- Pressure to complete "the last few percent" dies down as management
attention turns to more critical work.
- Latent defects may surface upon final inspection requiring re-work with no
added measurable product to show for the effort.
A report issued by the National Electrical Contractors Association (NECA) in
1983 further illustrates the general shape of the resource loading S-curve. Data
was collected from 40 different contractors on 54 building projects in 32 cities.
The projects represented four broad types of public buildings competitively bid
and which the contractors felt were typical of their business. The report includes
the supporting data which show the ranges of variation.
Figure 2 shows the overall average manpower consumption
rate S-curve for all the data collected (NECA 1983). The figure also shows the
overall low and high values and it is interesting to note that the range of variation
over a considerable number of projects is only 10% of the total time scale. It
should also be noted that a particular condition typically prevails in electrical
work on building construction. At the outset, only a small crew is required for
installing conduit and other electrical hardware during the course of work by
other trades. The bulk of the electrical work cannot be undertaken until those
trades are substantially complete. In other words, the work takes longer to open
up and accounts for a longer Stage 1 in this particular S-curve.
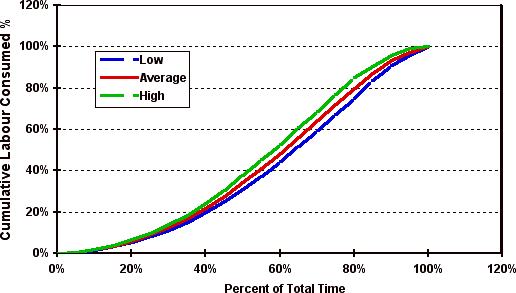
Figure 2: Cumulative manpower consumed for electrical systems installation
in new buildings -- NECA
1. From
the authorÍs personal records of progress tracking.
|